Halloween Spider Drop
Note: the text below is in response to a Halloween contest that the
project was going to be in a submission in. This project was made in
October 2008, and the original thread can be found here.
Well, I tried. Unfortunately, it wasn't strong enough.
My idea for OBCs contest was to have a human controlled spider thread
with a spider hanging on the end. I live in a dormatory, and we have a
central area four stories tall (~40 feet) with stairs on either side
and a central light shaft in the middle. The project design was to have
a person wave their hands in front of some IR devices, and that would
control the vertical movement of the spider, and how much it swings.
This way, the spider has a full 2d plane of movement. Also, a special
scenaro (when a hand got really close to the vertical sensor) would
drop the spider suddenly.
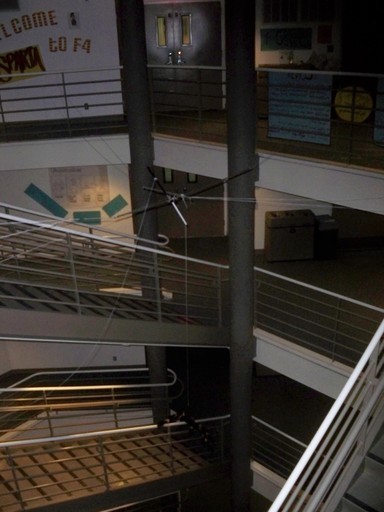 |
You can see the center
cross here, where the swing servo is mounted. This is just before I
took it down.
I'd just like to take a moment to say that my code works perfectly.
Rather, the problem that I ran into was my mechanical. The servos that
I used (Parallax standard and continuous) don't have enough torque (47
oz in), and so it created problems. My swing servo controlled the swing
by running the thread that the spider hangs from through a tube, which
was then attached to the servo. This servo was out in the middle of the
space, and mounted on some 1/2" angle iron for stability. Anyway, too
short of a tube, and I don't get swing, too long and it can't handle
it. Problem 1.
The second problem was the vertical movement servo. It's quite slow
under load, and it was a dull experience to raise the spider. To
suddenly drop the spider, I mounted the vertical servo on another
standard servo, which turned to drop so that the string would come off
the side of the drum. Imagine a roll of string. Stand it up, and it all
falls down. Anyway, apparently the friction is just a little bit too
much, and it didn't go out like I wanted. I could have filed it down, I
guess, but there were enough other problems that I didn't feel the need
to. |
The electronics consisted of a PPDB in side an old shoe box, with two
IR LEDs and two IR recievers. Also, I put in two 2.1mm Barrel jacks so
that I could provide seperate power for my swing servo and my vertical
servo. I had tested earlier, and found the regulator on the PPDB
getting hot.
As for safety, I took several precautions. Truth be told, I didn't
really get any sort of approval for this project, and it looked a bit
dubious with the liberal use of zipties. So, I took safety serious. All
components out in the air are very light, with gently rounded corners
so that they are fairly safe if it should fall. Next, I put lots of
sting out to the center. There are seven completely independent sets of
tie downs: two along the x axis, two along the z axis, one tied to the
cross point, one tied to the servo counter balance, and the spider
thread. Each of this were securely tied with a half hitch and a square
knot to various railings.
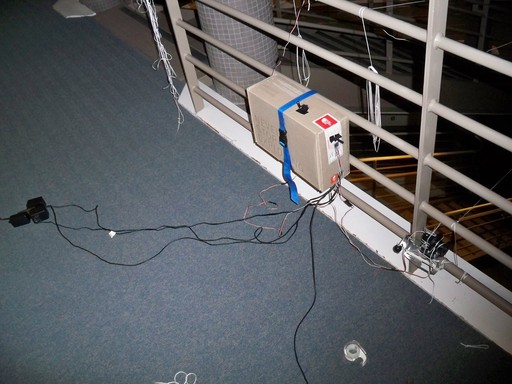 |
My control box with the
three power supplies and the vertical servo and drop servo mounted on a
BOE-BOT Chassis.
So, that was to be my submission. Next time (Christmas?) I'll try it
with stepper motors or maybe DC motors. Best of luck to everyone else!
|
Attachments
(Right click and "Save Link As...")
TestIrDutyDistanceDetector.spin
|
|